David's Ski Pick Trip - Rossignol
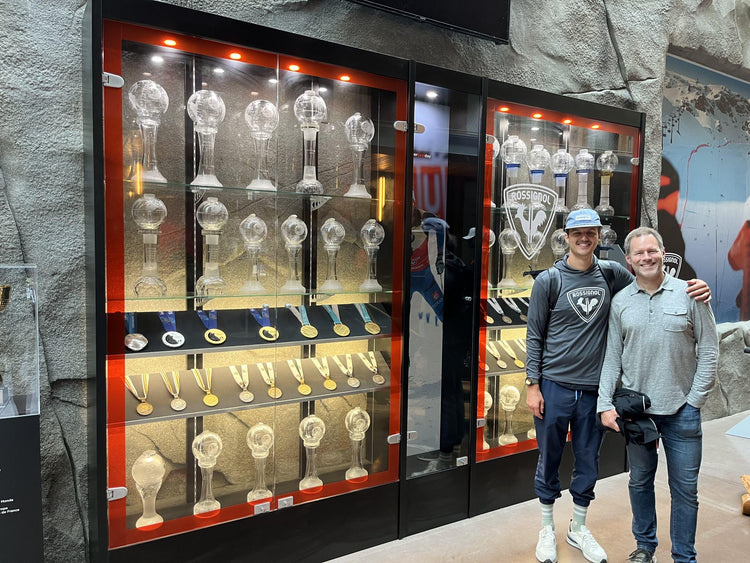
Rossi – Grenoble, France
by David Chamberlain
Picking trip 2024 is underway and the first stop this summer was the Rossignol French factory and warehouse in Grenoble, France.
Calling it a factory is a bit of a stretch as the production facility where they do a lot of their R&D and production of the high end ‘French’ skis is only two presses and a handful of workers with the capacity to put out only 10 pair a day. But the skis that they make here often find their way to the World Cup and become test designs for future production. The skis are built by hand very carefully at every step and can be very fast as a result, especially the classic skis. Rossi has another factory in Spain where most of the production skis are made.
My friend and former colleague Jeff Courter has recently taken over in France as the Race Product Manager and he did the planning and prep for my visit. It was great to see him and work with him again, and he seems to be having a very positive impact on the some of the operations here. Foss Kerker was also here picking skis. Foss was hired last year for domestic race service in the US. I was also able to meet and talk with Stefan Mouton and Julian Robert, both who play a key role in World Cup service for Rossi. Stefan does the grind development for the World Cup race skis and it was very interesting to talk with him.
The first day we spent picking skis in the warehouse and the star of the show was definitely the new SX skate ski. The skis were originally billed as a soft snow ski, but have since turned into an all around universal skate and the feedback has been very good. Julian showed us a lay up of a SX pair during our production facility tour. To achieve the ‘rounder’ camber, the material of the core of the ski is reduced at the tip and tail and the nomex honey comb is thinned. This allows the contact zones to be pushed back towards the bridge and for the core to flex more ‘smoothly’. The new top sheet that was put into use two years ago also plays a role in this along with a new sidewall design. The sidewalls are now made with a thinner three ply sheet, a sheet of wood that has grains that run vertically sandwiched between two sheets with horizontal grains. The wood used in the sidewalls is African Okoumé – this new design makes the sidewall lighter than previous Premiums. The cores are lighter and more flexible as a result. Sycamore is used for the rest of the wood in the core, mostly the sheet that runs under the nomex. Not sure what factors go into wood choice, most likely cost and availability, but the new layup of these skis seems to be working.
Day two we spent touring the production facility and offices. Julian gave us a tour and we were able to talk to the workers on the floor and see how the skis are layed up and pressed. We got to see the different molds up close. The CZ mold is used for the SX and S3, and the CU mold for the S1 and S2 skis. All classic skis are layed up in the CS mold. The process is always fascinating, especially the tweaks of the skis in the molds as they are heated in the press. I could watch the process all day long.
I have to give a big thanks to Rossi for the visit, especially Jeff and Foss. I stayed with Jeff and his family at their house up in Villard du Lans and we had some great French meals. This was the first year that we were invited to pick skis here and am already looking forward to next year.
Fischer and Salomon next week - I am spending the weekend in Lenzerheide, Switzerland while my wife attends the IBU meetings here Saturday and Sunday. My son Lucas is here and we will be hiking in the mountains looking for ruined castles…. Picking skis at Fischer starting on Monday morning….
Gear West Videos
How to Stop on rollerskis
Custom Insoles
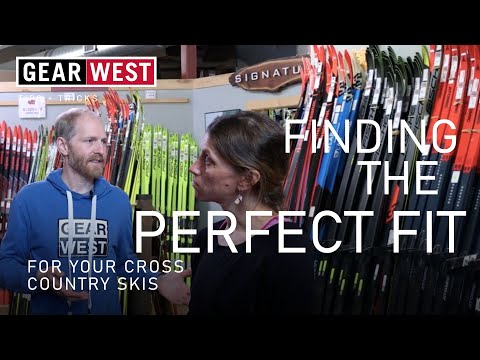
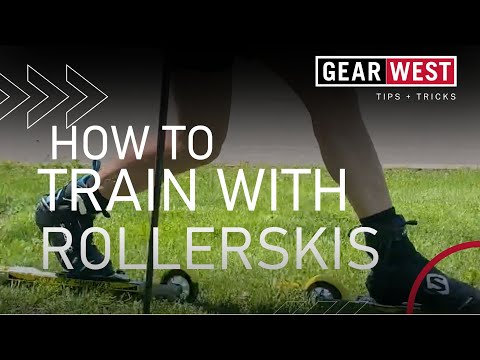
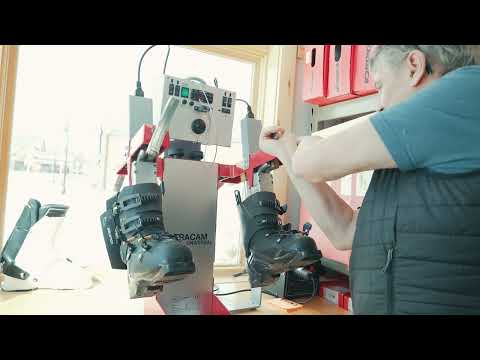